Blades in motion: Helicopter safety training helps RES team advance wind data monitoring
by RES | Apr 08, 2025 | Reading time: 5 min
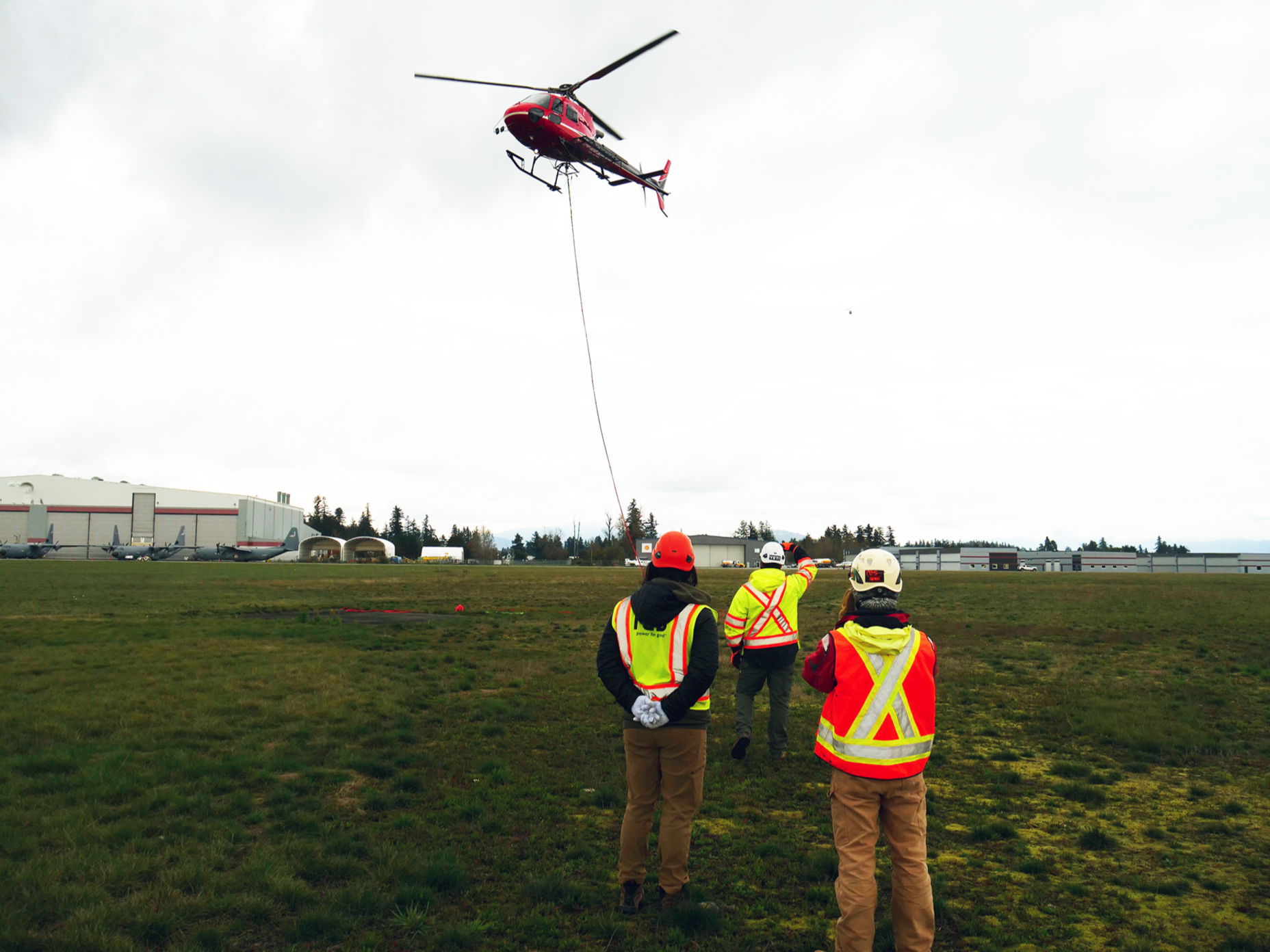
The journey of a wind energy project doesn’t begin with the first shovel in the ground; it starts years earlier, high above the land where future turbines might spin. Each potential project begins with a question: How do we know if this site has the wind potential to generate enough clean energy to offset the cost of constructing it, while sustaining a profit?
To answer this question, members of RES’ Technical Department embark on a meticulous discovery process, navigating remote terrain and utilizing cutting-edge technology to collect and analyze precise site-specific wind data.
“There are publicly available datasets, and we also have our own ‘mesoscale’ models to estimate roughly how much energy we should produce on a project site. But we’re capturing much more localized data, which is fed to our internal modeling,” said Zac Fish, instrumentation manager at RES.
This data allows the Energy Resource team to model realistic energy predictions based on factors like turbine type and placement. These improved predictions determine expected energy production, which guides project design and financial projections, such as anticipated revenue.
Accurate wind resource estimates also significantly influence a project’s financial predictability. By improving the accuracy of the data that RES’ analysis is based on, the financial outcomes of projects can be more reliably forecast throughout their entire lifecycle. This allows lenders to comfortably back projects at financing.
Measurement technology
RES utilizes two technologies to capture this critical information: met towers, which are free-standing 300-foot-tall structures that measure wind speed and other meteorological conditions with an array of instruments mounted at various heights; and vertical profiling Remote Sensing Devices (RSDs), with either Sound Detection and Ranging (SoDAR) or laser Light Detection and Ranging (LiDAR) technologies.
LiDARs used in wind measurements send beams of light upwards, which bounce off particles in the air. SoDARs work in much the same way, but use sound pulses that sound like pings or chirps. Unlike met towers, these devices are relatively compact, but they are complex, power hungry, and their deployment is no less challenging—especially in the middle of nowhere.
Helicopters help solve logistical puzzles
Getting sophisticated equipment into remote locations can be a logistical puzzle. Roads more often than not don’t exist, and carrying heavy equipment through dense forests or steep inclines isn’t practical.
“The biggest issue is: How do we get a remote sensing device with its power supply or the components of a met tower into the middle of a forest?” said Fish.
Some days, the answer is a grueling half-day trek using UTVs or snowmobiles to carefully navigate difficult access at a slow pace. On other days, the answer takes to the sky.
When the terrain is too unforgiving for ground transport, or if the distances are too great, helicopters become essential. Using longlining techniques, equipment is transported in nets or suspended on rigging, attached to a lifting line connected beneath a helicopter, dramatically reducing transport time and effort. Helicopters also ferry personnel in and out, saving precious hours spent trudging through difficult terrain and providing a safe and efficient emergency evacuation option.
In the last year alone, RES has installed five LiDAR devices and three 300-foot-tall met towers using helicopters in remote areas of Canada.
Enhancing safety and efficiency
Rory Curtis, director of energy resources at RES, has worked with helicopters for the installation of met towers and LiDARs/SoDARs across Canada since 2012. “Back when we started doing this type of work, we were applying crane principles to helicopter lifts, which while generally safe, didn’t fit all that well,” said Curtis. “There was also a reliance on the operator to confirm adequate performance, and the safety management aspects took a lot of learning, preparation and thought to get right.” Since 2012, Curtis has worked to refine the procurement, management and field operations of these types of work. He now manages both the Energy Resource and Instrumentation teams.
“We’ve got some really strong skill sets within the Instrumentation Team. I was looking for a way to properly share the knowledge I’ve gained over the years in a meaningful way so that we could get other team members positioned to manage helicopter operations safely and more independently,” said Curtis.
Some team members, like Wade Peterson, have decades of experience installing communication and cell towers across Canada, while others, like Fish, have aviation backgrounds. Fish, a former U.S. Air Force Fighter Jet Avionics Specialist with a degree in Aeronautics, understands aircraft limitations and the impacts of environmental conditions.
Curtis designed a syllabus and then worked with two highly experienced commercial helicopter pilots to put together a custom training course that would provide team members with the tools and knowledge they would need to safely manage and execute helicopter field operations. Four employees participated in an intensive three-day program, blending classroom lessons with real-world exercises with an Airbus AS350 helicopter.
Day 1: The team met with pilots in the classroom to discuss service procurement and flight safety, weather, and a pilot’s-eye-view perspective on complex operations, client interfacing, and insight into how operations could be designed efficiently and safely. In the hangar, the team familiarized themselves with the helicopter, loading and unloading passengers and cargo. Later that day, after a briefing on the task, the team practiced controlled entry and exit maneuvers with a helicopter in a low hover. They learned that every movement must be slow and deliberate, and that with training, it is possible to safely access areas without a developed landing zone.
Day 2: In the classroom again, the team learned about crew resource management, human factors in aviation safety, and the performance envelopes and characteristics of helicopters, particularly during lift operations. In the hangar, the team reviewed a large selection of helicopter lifting equipment, or “rigging,” including how to perform field inspections on components. The team reviewed redundant and fail-safe designs in equipment, and potential failure points in both equipment and operational practices. With the helicopter rigged for lifting, the team practiced working with the “long line” and safely attaching and receiving loads of material with the helicopter overhead.
Day 3: The final day covered aircraft maintenance, emergency procedures, and remote fueling operations. In the classroom, the team went over real-world examples of maintenance logs and how to correctly read and understand this documentation. The pilot instructors led an exercise reviewing case studies of flight safety incidents from the wider industry. In the hangar, an aircraft maintenance engineer guided the team around another AS350 helicopter undergoing significant annual maintenance. The team got familiar with control linkages, engine and powertrain components, rotor systems, and professional maintenance practices.
Fish describes the training as a pivotal moment for RES. “It was great for us all to get together and share our specific areas of expertise. Having this training ensures all our team members have the knowledge that allows us to continue operating with a very high degree of safety,” he said.
The RES difference
Innovation is what sets RES apart. Many companies specialize in just one aspect of wind energy—site selection, data collection, or equipment installation. RES does it all.
“We pride ourselves on innovation and forward-thinking. It’s what separates us from our competitors,” said Fish. “We can identify prime locations, capture precise data sets, design layouts, and safely install the measurement equipment ourselves.”
As the wind industry pushes further into challenging environments, RES remains at the forefront, finding new ways to measure, access and harness the power of the wind, whether in the air or on the ground.
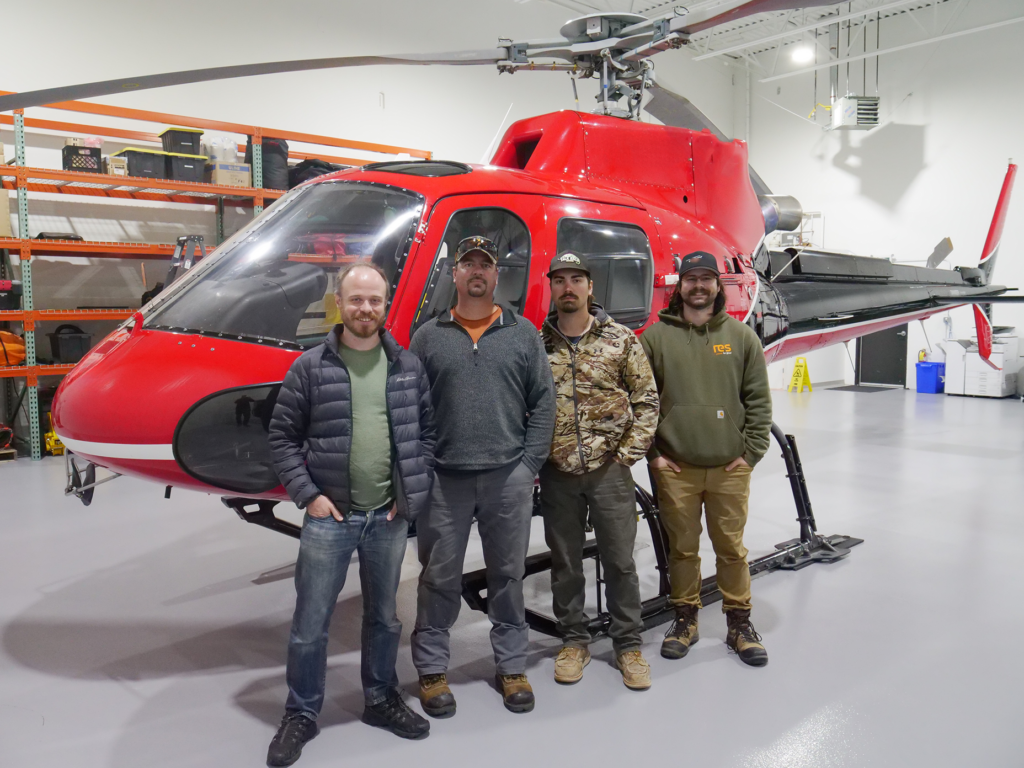
RES team members participate in a custom helicopter safety training course. From left to right: Rory Curtis, Wade Peterson, Dayton Halfmann, Zachary Fish