INTERVIEW: Big picture data – how we’re predicting the future
by RES | Oca 29, 2021 | Okuma süresi: 6 min
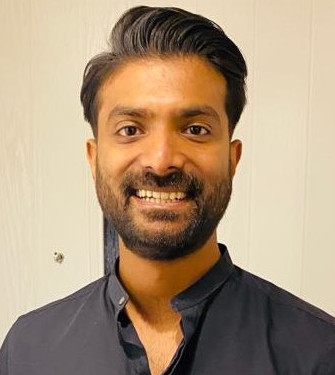
In a digital world where we are so dependent on data to make informed decisions, it’s no surprise that renewables are being optimised using real time data. However, what’s important is what data we gather and how we use it. That makes the difference between being a good asset O&M partner and being the best in the world. For us, it’s about paying attention to the smallest details that makes the biggest differences to the asset portfolios we manage.
In this double interview, Arvind Ganesan, based in the UK and Nicolas Ribaud from our French team explain how our Analysis and Optimisation teams use data to predict when assets need to be repaired and maintained to keep them producing energy efficiently.
What is Analysis and Optimisation Services and what do you do for clients?
Arvind: We analyse SCADA data produced by turbines and substations using our own custom-built technology agnostic software to analyse the performance the assets we manage.
We operate our analysis and optimisation service globally and across wind, solar and battery storage. The service helps clients and operators get a full understanding of the health of their assets to ensure adequate steps are being taken to maintain asset value and increase revenue.
Recently we were able to identify a defect on a Scandinavian wind farm. After an inspection to verify the data, we worked with the manufacturer which resulted in client savings in excess of £2.5 million.
Nicolas: We’ve introduced industry leading, in-house developed diagnostic tools and software to turn SCADA data into information which lets us make informed decisions. That means we analyse a range of data sources to provide early detection of the onset of a failure and underperformance and can then instruct our teams on the ground, or third parties where OEM full scope contracts exist, to go and fix those issues before they turn into bigger problems.
Getting a better understanding of the condition of assets, we optimise performance through targeted maintenance. This preventive and predictive approach minimises the impact of lost production – by reducing lead time for spare parts and pinpointing the best time to carry out any works. It also lowers cost – by reducing the number and severity of failures allowing in-situ repairs. And lastly it reduces risk – minimising physical checks and risk of catastrophic failure
What makes the service different from what an OEM provides?
Nicolas: Being independent to Original Equipment Manufacturers (OEM) enables us to identify all defects detected through condition monitoring. OEMs are ultimately concerned with availability, whereas we are focused on optimising the energy being produced.
We ensure a comprehensive view of the health of the site, irrespective of warranty periods, which provides owners with the information required to make maintenance and inspection decisions.
This service allows us to find defects before failure, therefore reducing the costs during the service period. It also helps OEMs – who we have very strong relationships with – improve availability as detection of issues early leads to less downtime.
In addition to the technical and financial benefits, the data we collate and analyse allows us to work with the asset management teams to ensure suitable measures are in place for the protection of wildlife and noise levels are kept within regulation during the lifetime of the assets.
Arvind: It’s also important to note that RES also has a history as an asset owner. That means our default mindset has been to optimise the asset value from day one of takeover.
We saw that RES operated sites were performing better than industry standard in availability and sub-optimal performance losses and so sought to investigate this further. We commissioned a study with DNV GL to independently establish this. The results showed that wind farms managed by RES perform 1% better than industry standard. DNV GL concluded that RES operated projects have much less sub-optimal performance than the industry standard benchmark. In fact DNV GL can hardly detect any sub-optimal performance on our projects.
The standard assumption is that sub-optimal performance reduces yield by 0.5%, which, on a 40 MW wind farm could mean £40k in annual revenue.
But sub-optimal performance is not as well understood in the industry as downtime. Owners may be losing revenue without realising even if the blades are turning. Looks can be deceiving. For example, if a turbine’s performance is curtailed due to a sensor issue, the blades may be moving (fulfilling the contractual obligation of the OEM) but they won’t be rotating at an optimal rate. Using real-time data, we can identify issues and fix them before they turn into larger issues leading to lost efficiencies.
So why is RES industry leading in detecting these issues?
Arvind: We have the tools and the capabilities to identify potential issues that OEMs cannot, and because we operate across entire asset portfolios, we’re always focused on creating efficiencies for portfolios rather than individual assets.
This also gives us access to huge amounts of data which increases the accuracy of our alerts which indicate when something isn’t right, and ultimately influences the decisions we then make to resolve issues at the site through our O&M teams.
Because we look at the entire asset ecosystem – from asset management to O&M, we have a vested interest in seeing assets optimised and generating as much energy as possible. The unique KPIs we have designed use SCADA data to tell us when something isn’t right. That means we’re not looking to create false alerts which aren’t accurate and waste the time of engineers.
We’re also constantly innovating new technologies and updating our tools to make them more sensitive and accurate. For example, power curve analysis. We used to manually check a turbine for efficiency, then we developed a tool to give us the answer remotely. We then programmed a baseline of “normal turbine behaviour” which our system can then use to run KPIs through. This generates irregularities, and means faults are more accurately detected, but they are also fewer in number and more reliable.
Why do clients use your services above anyone else? What makes RES different?
Nicolas: Our team combines a range of vibration, oil condition and temperature data to analyse the condition of wind turbine main bearings, gearboxes and generators. It’s like giving your car a thorough MOT every second of every day.
These activities are crucial to prolonging the life of the asset and getting as high a yield as possible while minimising unnecessary downtime by identifying issues early and addressing them through targeted maintenance and forecasting. Much like a chip in your car windscreen – fixing it when it’s small could save you from considerable pain later. It is therefore important to be careful when identifying and dealing with problems to maximise energy production.
Arvind: We always aim to be a step ahead. To give an example – we were brought onto a site where the OEM was previously responsible for monitoring the turbines. Damage occurred inside a turbine gearbox, causing a complete shutdown of the asset and lost production resulting in £98k of costs.
Reviewing the data from the turbine and using our technology and monitoring expertise, we identified the early warning signs and used this to monitor other turbines on the site. A further turbine was identified to also have a defect. The expertise in our team meant the turbine was able to continue operating while replacement work was planned, preventing weeks of downtime, allowing us to plan replacement works in low wind, and save money in components and labour. The component could be replaced and refurbished due to the stage of damage it was at, as opposed to being scrapped in the case of the first turbine.
Using sophisticated in-house algorithms, our O&M team can identify issues, raise this with the asset management team and implement preventative or restorative measures within planned maintenance times, if possible, or even to replace faulty parts within their warranty period.
The impact of this shouldn’t be underestimated – it could be the difference between a minor inconvenience and a substantial repair bill. Thanks to our significant experience in this area, we have the evidence to back that up.
Are you using AI to improve efficiency in any way?
Arvind: Yes we are. Our predictive maintenance is made possible by machine learning models which we have developed in-house. The models have been designed to mimic a typical energy asset and aim to pick up anomalies in CMS data.
Bespoke KPIs are created for different sites – taking into consideration historic maintenance events and current performance to give us a full picture of what to expect in the future. We also pool data from other similar assets we manage in order to maximise our chances of predicting issues before they happen.
This is true machine learning at work – gathering lots of data and ultimately letting the system make suggestions for maintenance events.
Nicolas: We are also currently working on a SMART reliability project which will provide a single interface combining all reliability analysis – including machine learning analysis – from around the world to allow our engineers to be as reactive as possible when detecting faults.
It is our intention to use machine learning to continuously improve our decision making, and ultimately keep our clients assets optimised and producing as much energy as they possibly can.
What’s the difference between the UK&I and France when it comes to this service?
Arvind: Not a lot – apart from maybe the language spoken in our teams!
Our service is a global one. Many of our clients have portfolios spread across multiple regions so being able to work with us and use a global system which has a consistent service is important.
We have teams around the world providing analysis and optimisation using the same tools and systems we have produced in-house. That means we’re aligned in terms of regulations, processes and tools – all to the benefit of making our clients assets work smarter, not harder.
For more information visit https://www.res-group.com/en/services/operations/
or watch our latest short film at https://www.youtube.com/watch?v=ty3U14zkEiQ