Solutions
Our passionate and experienced people deliver successful clean energy projects globally.
Technologies
Driving a clean energy future through state-of-the-art renewable technologies.
See all technologiesResources
Browse our latest resources, including company updates, customer stories, industry insights, and research reports.
See all resourcesCareers
Join a collaborative team of passionate individuals who engage in meaningful, stimulating, and world-changing work.
Learn moreAbout RES
We live our mission, celebrate the people making it happen and transform the way the world produces and consumes energy.
See about usOur offices
Like our business, we’re truly global – but proudly local. Find contact and location details for every RES office.
Contact us-
Home
/
Resources
/
Case Studies
/
Anemo Analytics: unlocking the power of data to enhance wind farm performance
Anemo Analytics: unlocking the power of data to enhance wind farm performance
by RES | Jan 22, 2024 | Reading time: 2 min
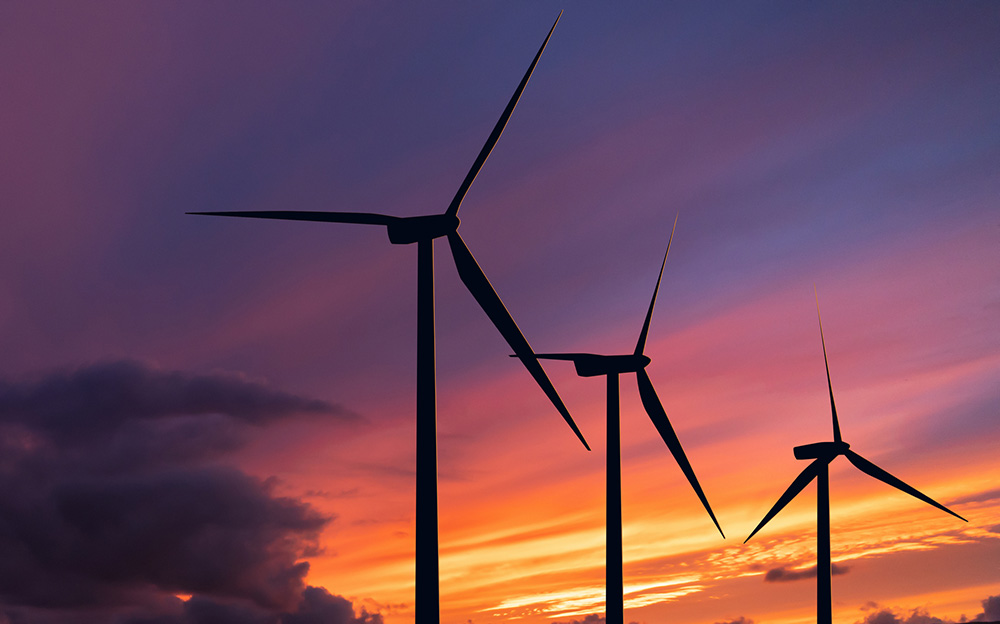
White Creek Wind Farm, which began commercial operation in 2007, is a 205MW wind farm in eastern Washington state consisting of 89 Siemens 2.3 MW wind turbines. Its sister site located nearby, Harvest Wind Farm, began operating in 2009 and produces 99MW from 43 Siemens 2.3 MW wind turbines. Together they are capable of powering over 100,000 homes.
NAES, the operator for both sites, had been using standard low frequency SCADA data to support its operational decisions, but was also aware that accessing and analysing the two sites’ high frequency, raw turbine controller data would provide a much clearer picture of asset performance, health, and efficiency. Keen to tap into the benefits of accessing this type of data to increase value for the owner, NAES engaged Anemo Analytics.
The Work
Blending wind turbine engineering domain competence with physics-based advanced analytics models, Anemo Analytics conducted a full diagnostic health check of all 132 turbines across the sites, utilising the existing raw high frequency controller data from the turbines. No dedicated measurement campaigns or additional hardware on the turbines were needed.
The health check revealed several turbine controller parameter settings that could be optimised. It also identified significant single pitch rotor imbalances and mass imbalances in need of correction to manage fatigue loads and mechanical main component failure rates.
It is important to note that original pitch calibrations are made under the assumption that each turbine blade is identical. However, the blade manufacturing process is not precise enough to ensure this and other factors, such as vortex generators falling off, can also influence individual blade performance. In addition, standard operational wear-and-tear makes proper blade balancing difficult, as technicians are left with imprecise mechanical markers for the annual alignment procedure. In this instance, the result was unbalanced lift, causing drivetrain vibration and possible damage for a range of the turbines on site.
Anemo technicians prepared a detailed report of their findings, complete with recommendations for every sub-system, component and sensor issue on each turbine. While some corrections could be made remotely, Anemo also armed NAES’ onsite technicians with field corrections that could be made to further improve turbine performance. The report also showed how these processes could be bundled into the annual service schedule.
Once parameter settings were optimised and pitch calibrations completed, a new and more healthy performance baseline was established for each turbine. Following this, additional performance enhancements were explored, including resolving aerodynamic yield underperformance, mitigating yaw overload, identifying pitch hydraulic cylinder seal leaks and incomplete power curve upgrade kit installations i.e., missing vortex generators.
Results
Using Anemo’s recommendations, NAES implemented an optimum pitch correction for three blades to balance out the differences in blade aerodynamics and excessive loads. The adjustments made from the initial health check report resulted in reduced turbine fatigue loads, which in turn reduced component failure rates and increased asset lifespan. The recommended performance enhancements not only resulted in increased annual energy production from the resolved yield-underperformance issue, but also ensured that there was no lost production from possible turbine downtime.
The recommended performance enhancements resulted in an additional output of 6,000 MWh over 12 months, creating approximately $360,000 in additional revenue.
The success of the initial project has resulted in NAES deploying Anemo’s solution on a continuous basis, with the team now receiving ongoing asset optimisation and operation and maintenance recommendations in real-time.
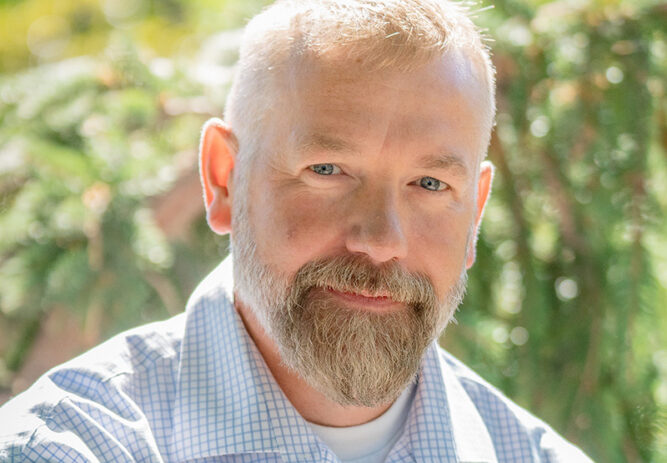
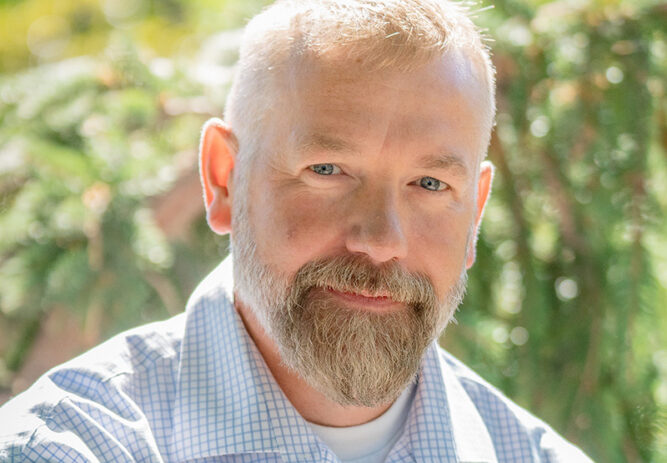

We have been working with Anemo now for over four years to help improve the performance of the sites that we manage. Anemo’s analytics have enabled us to identify when a turbine requires preventative maintenance, recalibration and identify issues that require further investigation. Ultimately, Anemo has helped us to reduce downtime and OPEX costs for our customers.”
Bjorn Hedges, Plant Manager
NAES