Data as the path to lower operating costs and higher performance
by RES | Apr 02, 2025 | Reading time: 4 min
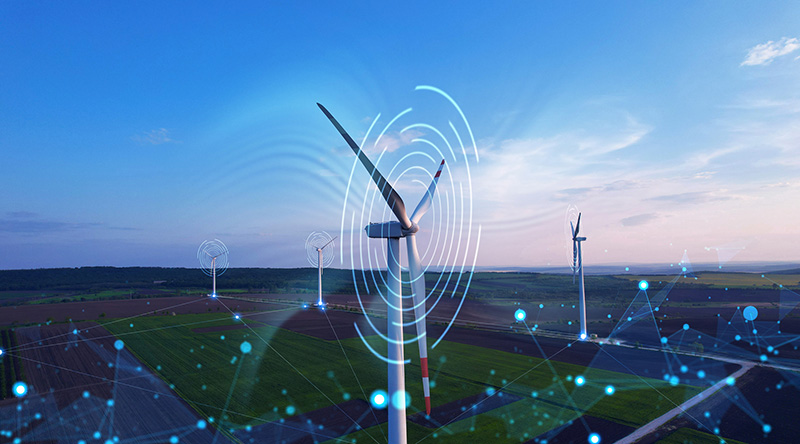
It’s a challenge every wind farm operator wants to overcome – how do you lower operating costs and increase performance, whilst still maintaining reliability and high safety standards? It might sound like an untenable goal, but it can be achieved. And data is the key to unlocking the possibility.
Achieving higher performance and lowering OPEX is always desirable, but even more so in times of geopolitical uncertainty, supply chain challenges and higher interest rates, where securing predictable, high-quality returns on investment becomes even more critical. The best starting point for achieving this is by harnessing the power of the data generated by your assets, enabling greater transparency, deeper insights into turbine performance and smarter decision-making.
What if we could produce more power from already existing assets?
Wind turbines create a lot of data, and it’s likely that most, if not all, operators are already using some of this data to gain performance insights. However, many are likely relying primarily on low-frequency SCADA data, which provides only a partial view of performance. For those operating a multi-brand fleet, the challenge is even greater, as there are no unified data access standards, leading to inconsistencies in data availability and quality across different turbine models.
High frequency data and analysis
The key is leveraging high frequency data, which typically operates at a rate of 15 times per second and provides around 3000 tags. In comparison, SCADA provides a partial view (usually 100 tags at ten-minute intervals, or occasionally 300 tags at one second intervals, if access to 1-sec OPC data is enabled), offering only limited and aggregated snapshots with significant gaps in between.
Though still valuable, this limited perspective can mean that emerging issues go unnoticed until they reach a critical level.
Solutions like AnemoLive enable operators to access high frequency data at both individual turbine and fleet levels. This enhanced level of detail helps detect anomalies early, allowing for proactive decision-making that can extend the lifespan of minor and major components. It also supports more efficient planning of predictive maintenance and shutdowns. However, data alone won’t help you achieve your goal. It must be properly interpreted, and crucially – insights must be acted upon.
Specific turbine model domain knowledge and expertise are essential to interpret this data and transform it into meaningful insights. Solutions like AnemoLive not only provide access to high-frequency data but also integrate expert analysis, where remote diagnostics, validation, and interpretation come together to deliver actionable recommendations for operators.
Once these insights are uncovered, how can operators implement them to achieve lower OPEX or higher performance? Depending on the findings, there are several ways to realise cost efficiencies.
Blade services
Blades are frequently a source of issues due to the constant forces acting on them. If analysis indicates a blade problem, a high-quality inspection is a valuable next step. Solutions like 3DX, which utilise autonomous drone inspections, enable 100% coverage of blade surfaces, providing a detailed assessment of blade health quickly and without requiring technicians to climb the tower, reducing associated safety risks.
Once again, the power of data and domain expertise comes into play. The data collected can be analysed using a combination of AI technology and expert insights to identify potential issues. Minor repairs can then be scheduled before they escalate into major failures. If issues appear to be potentially critical, additional advisory expertise – such as that provided by Bladena – can be brought in to offer solutions that mitigate risks, including their range of patented hardware upgrades and proactive maintenance strategies.
Parts supply and refurbishment
The proactive maintenance of both minor and major components is another key action that can help lower operating costs. By optimally scheduling maintenance and planned shutdowns, operators can minimise downtime and its associated impact. The earlier potential issues are identified, the easier it is to plan mitigation, ensuring that replacement parts are available when needed, without delays.
Component replacement can be a significant expense, but costs can be reduced by opting for refurbished components rather than new ones. This can be a highly cost-effective solution, and RES’ spares and repairs capability ensures operators have the necessary supplies when they need them, in a reliable and cost-efficient manner.
Ongoing optimisation and energy yield enhancement
Using high frequency data as part of continuous monitoring is not just about identifying anomalies early on across the operational life of an asset, it’s also about identifying opportunities to enhance Annual Energy Production and maximise returns on investment. Once again, combining data with deep domain expertise and software and hardware solutions can boost performance beyond original factory defaults. This can be particularly valuable on ageing assets where performance has degraded over time and new advances allow significant improvement. Data-driven insights can be combined with optimisation of settings and parameters through tools like TuneUp or DynamicYaw and complemented by hardware upgrades like AeroUp to unlock this value. These solutions allow operators to optimise the turbine controller, wake steer and blade aerodynamics in a way that improves energy yield in a sustainable and reliable manner.
Tailored solutions to meet individual operator needs
Lowering operating costs and improving performance is an achievable goal, and the level of success depends on a number of different factors. Data is the first step to unlocking the potential, but it does take a combination of many insights, decisions and actions to get the best return, and this will vary depending on the individual situation, from a single turbine to a large portfolio of assets. Navigating this path as an operator may sound daunting, but partnering with a business like RES can make that journey a smooth one by providing end-to-end solutions that enable operators to have a simple interface with one provider. This holistic and scalable approach is designed to make things easier for the operator so they can focus on making clear and informed decisions with the confidence that it can be actioned by a trusted partner.
An easier relationship that brings transparency, confidence and results. Surely that is the goal for every operator?