Services
Technologies
Promouvoir un avenir énergétique propre grâce à des technologies renouvelables de pointe.
Voir toutes les technologiesRessources
Parcourez nos dernières ressources, notamment les mises à jour de l'entreprise, les témoignages de clients, les informations sur le secteur et les rapports de recherche.
Voir toutes les ressourcesCarrieres
Rejoignez une équipe collaborative de personnes passionnées qui s'engagent dans un travail qui a du sens.
CarrieresÀ propos de RES
Nous vivons notre mission, nous mettons en avant les personnes qui la réalisent et nous célébrons les transformations qui changent la façon dont le monde produit et consomme l'énergie.
Voir à propos de nousEmplacements et bureaux
Tout comme notre entreprise, nous sommes véritablement mondiaux – mais fièrement locaux. Trouvez les coordonnées et l’emplacement de chaque bureau RES.
Nous contacter-
Accueil
/
Resources
/
étude de cas
/
Ultrasound & Measurement Inspection
Ultrasound & Measurement Inspection
by RES | Juin 28, 2023 | Temps de lecture: 2 min
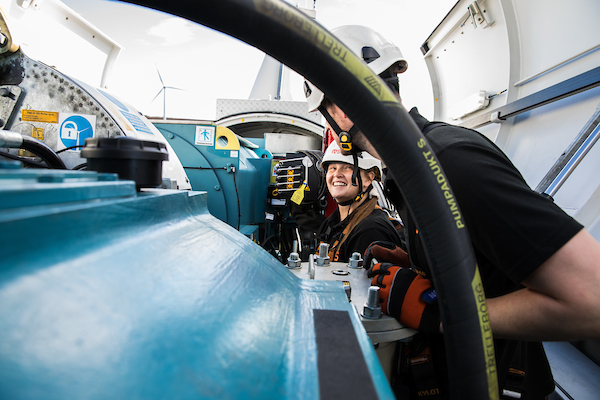
RES was asked by a wind site owner to complete a blade bearing ultrasound and measurement inspection for a wind farm located near Edinburgh in Scotland.
The existing operator was aware that there were defects on the site, but the full extent wasn’t clear meaning that planning future works was difficult. Whilst RES does not operate or maintain this site, we are one of only a handful of O&M providers that provide a Blade Bearing Ultrasound and Measurement Analysis Service. Despite ultrasonic testing of mechanical and electrical systems being widely used in other sectors, its use within onshore wind is still relatively new.
RES has utilised this method for several wind farm owners and operators to help verify issues being highlighted by their existing O&M contractors, as well as to help plan future works on O&M contracts.
We have also used the technique to verify issues for clients and have been proven successful in identifying lubrications starvation and bearing defects.
The work
RES completed a blade bearing ultrasound and measurement inspection across the site which consists of 25 Nordex N80 2.5MW turbines – 75 blades in total.
This type of inspection provides a predictable diagnostic capacity due to its high frequency and short wavelength which easily filters out background noise and focuses in on a relevant component. When changes begin to occur in the ultrasonic range, there is still time to plan appropriate maintenance.
Ultrasonic testing is particularly useful for fault diagnosis on slow moving bearings and low-level vibration which can’t be picked up by other nondestructive testing (NDT) methods. This makes it extremely useful to use on blade and main shaft bearings as well as hydraulic and electrical faults.
Results
RES helped the existing operator understand the full extent of existing defects in order to plan future works.
Following our survey, we found 19 defects and categorised the level of wear indicated to show which bearings require attention more so than others. We provided a full report to the existing operator who could then complete further assessments and plan future works to avoid more serious failures occurring and revenue losses for the owner.
Follow up inspections are planned in the future to help manage the progression of possible failures and assess the effectiveness of the remedial works carried out following the initial inspection.