Castlecraig transformer replacement
by RES | Avr 28, 2023 | Temps de lecture: 3 min
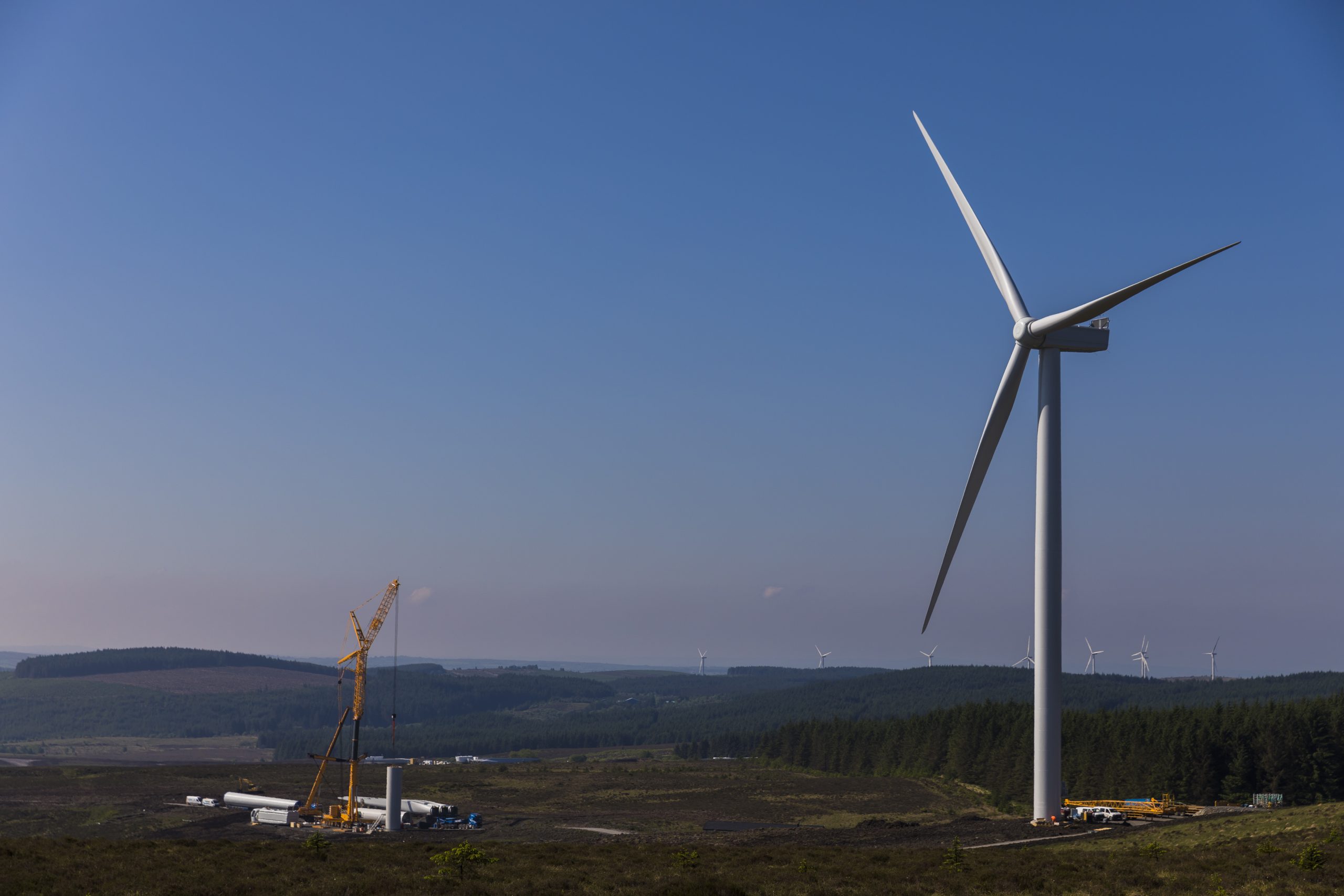
Castlecraig Wind Farm is a 25MW project located in Co. Tyrone, Northern Ireland. Its 10 wind turbines have been producing enough clean energy to meet the needs of over 18,500 homes since its construction in 2018. The Project is owned by sustainable infrastructure investors NTR and forms part of their NTR Wind 1 LP fund. Costing £50 million the project was constructed by RES, who continue to provide asset management services.
In early October 2020 our asset management team received a real time alert that a transformer on one of the turbines – the link between the wind turbine and the distribution grid – had failed. Ensuring the turbine was repaired quickly and safely was of the utmost importance to RES and NTR.
The work
The asset management team at Castlecraig got in touch with Nordex, the OEM (original manufacturer) of the turbine to investigate the issue and request a replacement transformer was available if needed. The asset management team then ensured everything was in place for a rapid replacement which involved coordinating with a host of local and national contractors.
In just over two weeks the replacement was complete. Typically, a replacement transformer may take much longer to source and replace. The rapid fix involved a host of teams working across weekends and out of normal working hours to get the turbine back up and running. Steps were also taken to ensure a similar issue would not happen again in future.
During the outage required to replace the transformer RES and NTR identified areas of the site infrastructure that could also be inspected and took the opportunity to review the high voltage switch gear of all the turbines and connections which had recently been flagged as a possible safety concern. All turbines on site were checked and no issues remain.
The replacement was conducted during the COVID-19 pandemic which presented its own unique challenges and ensured the highest levels of site safety and coordination between contractors. Only one contractor could be present in a certain area at any one time. Normally there would be less than 100 man hours during this period but with all the work taking place, there was over 1,000 man hours for the month.
Several contractors were involved to successfully replace the transformer. These included Nordex, EPS, Simkiss, Sweeney Scaffolding, Windtranz and Quinn Crane Hire amongst others.
The challenge was ensuring we were working together focused on the same goal but remaining safely apart and communicating at all stages of the replacement. Daily Toolbox talks were held to ensure everyone was aware of who was working in each area and to ensure each and everyone went home safe.
Results
David Brolly, Asset Manager at RES, said: “Thanks for our excellent relationship with Nordex, we were able to overcome the problem very quickly and get the turbine running again in just over two weeks. When there are any issues on site, being able to call on contractors and work together quickly and strategically is essential to ensuring down time is kept to a minimum.”
“Our client NTR was extremely satisfied with the speed the replacement was arranged. We were in constant contact with NTR and ensured they were aware of the progress. As the turbine was under warranty, no costs were incurred, and lost production time was reduced to only two weeks including carrying out extra services to reduce further downtime. Given we did all of this during the height of the pandemic is also testament to the professionalism and commitment of our team and the contractors we work alongside.”
Clive Gordon, Local Operations Manager at Nordex, said: “An internal transformer replacement is a complex task that involves multiple contractors working on behalf of Nordex. Our major component team planned and executed this task alongside our contractors in a period that had a limited impact on the overall downtime of the turbine. Safety of course is our number one priority, and to get the repair complete during the pandemic safely and in a timely manner is testament to all involved with the working restrictions that were in place.
“The work was completed under CDM regulations and managed by our local team in conjunction with our major component team. We had planning calls with RES in the week leading up to the replacement; any issues or concerns were dealt with appropriately and before work started. This ensured there would be no time delays that would further affect availability.
“The strong working relationship developed with RES locally over the past 12 years definitely helped in the planning and executing of this task.”
Partager cet article
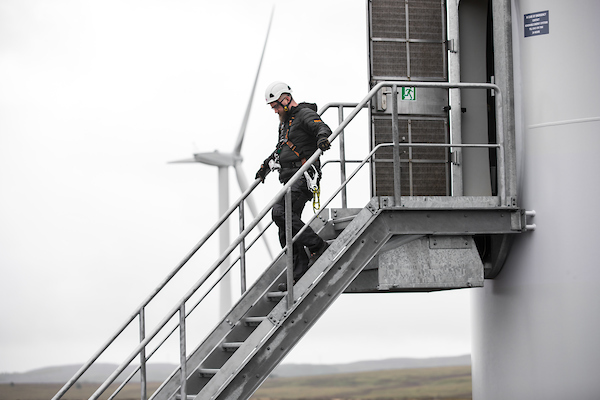
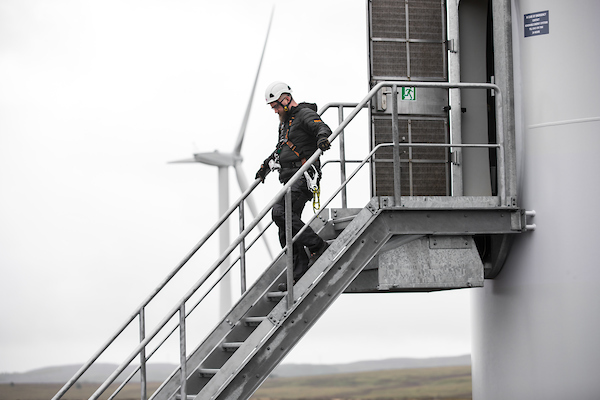

Thanks to the professionalism shown by our contractors, RES and Nordex, the replacement of an internal transformer at Castlecraig was completed in just 2 weeks. The fact that this was done safely is of upmost importance to NTR. The teams had the added complexity of the ongoing global pandemic to deal with and it was important that protocols were followed. NTR will always prioritise safety before speed however when you have experienced contractors working to a high standard, we see that both can be achieved. I would like to thank all involved for a job well done.
Kieran Tubridy, Senior Asset Manager
NTR