Qué hacemos
Nuestro personal, apasionado y experimentado, realiza con éxito proyectos de energía limpia en todo el mundo.
Tecnologías
Impulsar un futuro energético limpio mediante tecnologías renovables de vanguardia.
Todas las tecnologíasRecursos
Consulte nuestros recursos más recientes, incluidas actualizaciones de la empresa, historias de clientes, perspectivas del sector e informes de investigación.
Ver todos los recursosCarreras profesionales
Únase a un equipo colaborativo de personas apasionadas que realizan un trabajo significativo, estimulante y que cambia el mundo.
Más informaciónSobre nosotros
Vivimos nuestra misión, celebramos a las personas que la hacen realidad y transformamos la forma en que el mundo produce y consume energía.
Sobre nosotrosOur offices
Al igual que nuestro negocio, somos verdaderamente globales, pero orgullosamente locales. Encuentre los datos de contacto y ubicación de cada oficina de RES.
Contacto nosotros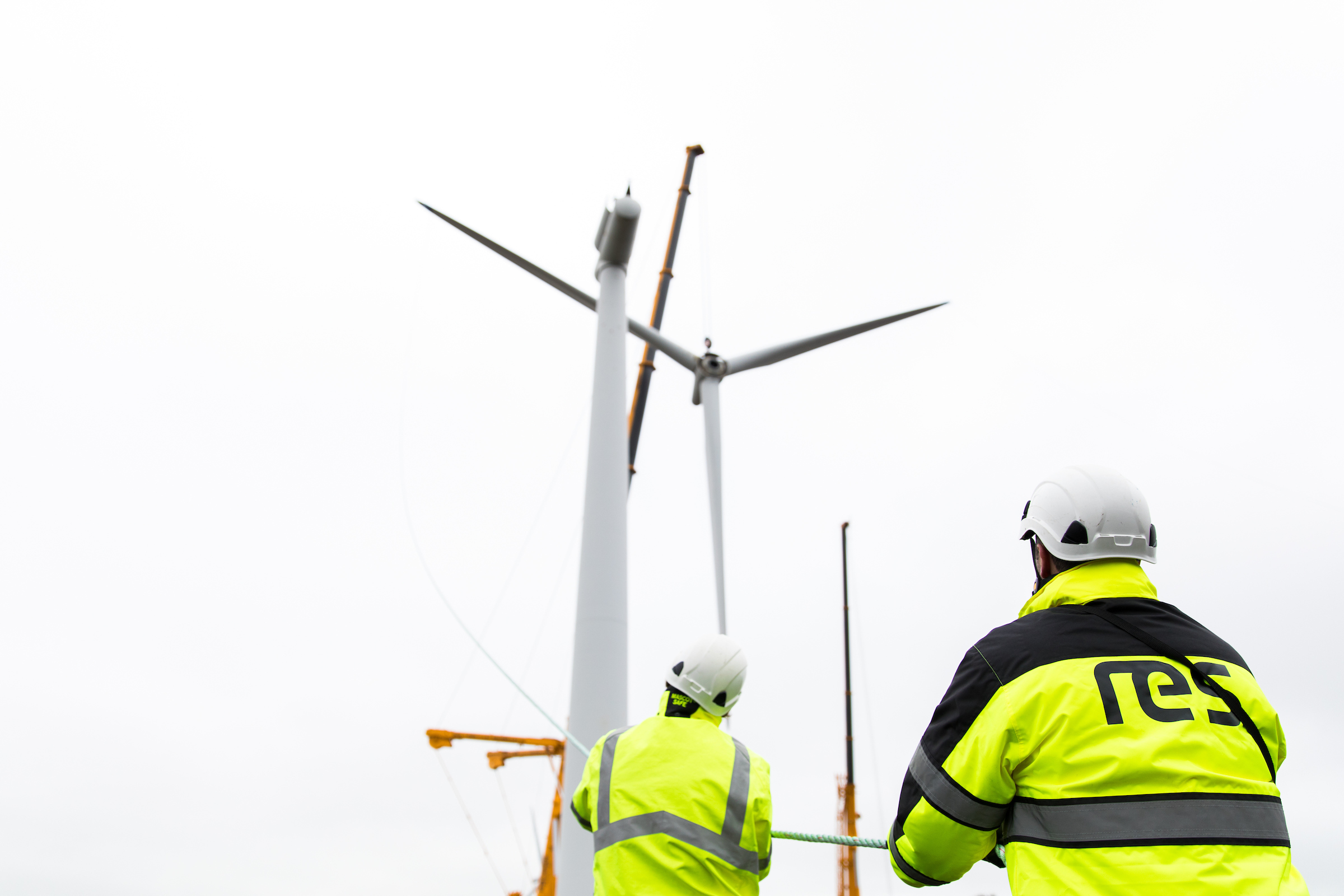
Por Brian McDaid, Jefe de Operación y Mantenimiento de Turbinas, RES
Las fallas de los componentes principales son habituales en la industria eólica, a punto tal que RES cuenta con un equipo entero dedicado a reemplazarlos. No es que los componentes principales (cajas de engranajes, rodamientos o generadores) sean especialmente propensos a averiarse, es que ahora hay tantos en funcionamiento que las fallas forman parte de las operaciones y el mantenimiento de los parques eólicos.
Los plazos de entrega de algunos componentes oscilan entre tres y seis meses, por lo que es fundamental pedir las piezas con antelación. Una falla inesperada puede provocar tiempos de inactividad significativos, lo que se traduce en costosos gastos de reparación y grandes caídas en los ingresos y el rendimiento reduciendo (en consecuencia) la energía renovable suministrada a la red, con pérdidas sustanciales en general.
Integración de técnicas nuevas y tradicionales de inspección
La introducción del sistema de control basado en la condición ha ayudado a revolucionar la industria, permitiendo a los equipos de mantenimiento de parques eólicos alinear los componentes de repuesto antes de que se produzca una falla, sin tener una costosa reserva escondida en un almacén.
En el parque eólico de Taurbeg (Irlanda), por ejemplo, nuestro sistema interno de control de estado detectó un problema en el eje principal de uno de los aerogeneradores de 2,3 MW. El plazo de entrega del componente fue de nueve meses. Afortunadamente, como el problema se detectó pronto, el reemplazo se pudo planificar cuidadosamente y se evitó una falla catastrófica. Como resultado, la turbina estuvo fuera de servicio menos de una semana (en lugar de varios meses) lo que ahorró al cliente £120.000 en lo que podría haber sido una pérdida de ingresos.
Un factor decididamente más humano para evitar la falla de los componentes principales es el poder de la atención a los detalles. Muchos ingenieros experimentados sabrán si una lectura de aceite no es del todo correcta o si algo suena mal: identificar y resolver problemas menores a tiempo suele ahorrar mucho tiempo y dinero a largo plazo. Esta es una habilidad que debemos transmitir (conscientemente) a la próxima generación de ingenieros de aerogeneradores y una de las muchas razones por las que somos tan proactivos en la capacitación de aprendices, la mejora de las cualificaciones de nuestra plantilla y el fomento de un lugar de trabajo genuinamente inclusivo y familiar.
Aunque lentamente los sensores están pasando a digitalizar esta increíble habilidad, aún no ofrecen una imagen completa. En RES combinamos los conocimientos sobre sensores y la experiencia en ingeniería con técnicas más inusuales, como los ultrasonidos y la inspección por medición. Esta técnica de inspección es especialmente adecuada para detectar posibles fallas y necesidades de mantenimiento en rodamientos de movimiento lento y en componentes con bajos niveles de vibración. En una inspección reciente de 75 palas, pudimos detectar 19 defectos que, de otro modo, no se habrían detectado con ultrasonidos.
La ventana meteorológica tiene la última palabra
Una vez identificado la posible falla de un componente principal, empieza a correr el reloj de la sustitución. El tiempo se convierte, entonces, en el mayor reto del equipo de mantenimiento. Si va a sustituir una pala, por ejemplo, querrá que el tiempo sea casi completamente inmóvil: está diseñada para atrapar el viento, ¡pero eso no es lo que quiere cuando está en la grúa! Dado que los parques eólicos suelen estar situados en lugares con velocidades medias del viento más elevadas, puede ser difícil encontrar una ventana meteorológica de tres o cuatro días durante la cual una grúa móvil pueda ayudar con seguridad al reemplazo, y en la que el tiempo de inactividad tenga el menor impacto en los ingresos.
El equipo vigila de cerca las condiciones meteorológicas y se mantiene en contacto permanente con el operador de la grúa, para garantizar que solo se movilice cuando las condiciones meteorológicas permitan un trabajo seguro. A menudo, la decisión de seguir adelante solo se toma con 24 a 72 horas de antelación. Que una grúa llegue al sitio, pero no pueda operar es un error costoso que ha dado lugar a algunas innovaciones interesantes a tener en cuenta, como las grúas que se construyen directamente en la torre de la turbina y que pueden operar con seguridad a velocidades de viento más altas. Además, el software meteorológico avanza sin cesar, ayudando a los operadores de activos a predecir mejor las condiciones meteorológicas cambiantes y a superar la naturaleza incontrolable del tiempo. El reemplazo de los componentes principales es un arte que combina la innovación en inspección y control con un profundo conocimiento de la industria. Un reemplazo bien ejecutado puede ser la diferencia entre tener una turbina fuera de servicio durante varios meses, con un costo de decenas de miles de libras, o planificada para solo unos días en un mes en el que la producción estará en su punto más bajo. Aunque es improbable que lleguemos a ver un invento que controle el viento, con lo que está en juego, merece la pena contar con un equipo altamente calificado que pueda detectar la falla de los componentes principales antes de que se produzca y que ofrezca un amplio margen de maniobra para reemplazarlos