Bucking the trend in solar
by RES | Nov 11, 2022 | Lesezeit: 6 min
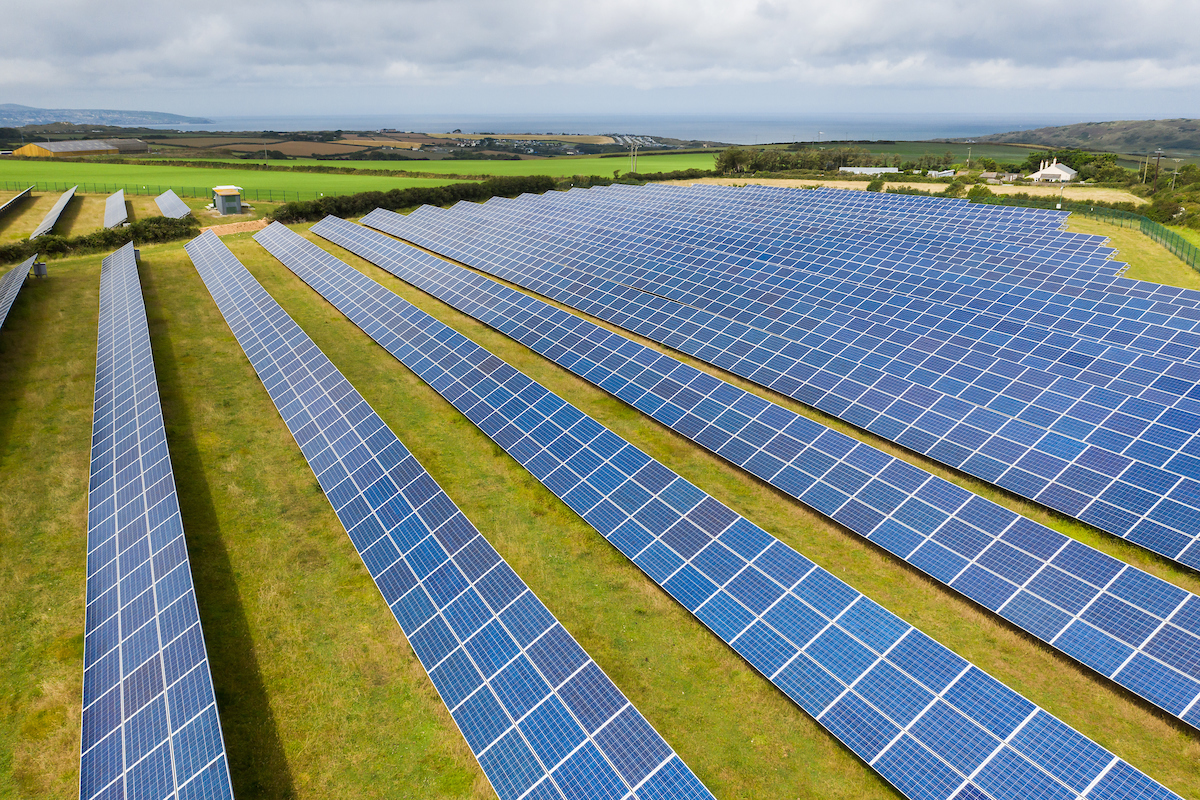
Solar PV technology is the cheapest it has ever been, driving global installation rates to new highs. According to a recent report from SolarPower Europe, global solar capacity has doubled since 2018, bringing the world’s solar fleet to more than one Terawatt in capacity. With the urgent need to meet net zero, enhance energy security and reduce bills for consumers, it is expected that this trend will continue with solar capacity installations on track to grow by 30% globally this year and more than double to 2.3TW by 2025.
However, recent reports have suggested that whilst the technology is undergoing huge growth, the average downtime of assets has increased. This is being partly attributed to supply chain issues. GCube, specialist insurers for utility-scale renewable energy projects, have predicted a rise in claims as contractors face pressures to stretch resources and drive down their costs to capture emerging opportunities.
Increasing project availability
Despite the reports of increased downtime, we are finding that the global portfolio RES manages is bucking this trend. For instance, across one portfolio managed by our team we have increased availability by over 5% since we began managing the site. On another portfolio we have seen an increase in availability as well as a 5% increase in the Energy Performance Index (see figures 1 and 2).
Figure 1 – Value Improvement Plan leading to sustained improvement in portfolio availability
Figure 2 – Value Improvement Plan leading to demonstrable improvement in Energy Performance Index (EPI)
So, what’s our secret and how can we collectively reduce downtime across the industry to ensure we deliver the cost, energy security and environmental benefits of this technology?
One of our recent successes has been the implementation of our Enhanced Spares Management service. In the UK&I for instance, we have found that inverter faults are causing significant downtime. This is partly because inverters are complicated and have numerous sub-components, each of which could be vulnerable to failure. In addition, we have also come across inverters managed by other operators who have not complied fully with the equipment maintenance requirements. Due to recent global events, the lead time for spare inverter parts has increased substantially, which can lead to excessive downtime if the spare part is not readily available. Our Enhanced Spares Management service, in which we hold thousands of different spare parts for our clients and deliver these within a guaranteed time period, was implemented to mitigate this risk. This service is regularly avoiding our clients incurring lost revenue due to parts shortages. It’s not just the holding spares though, it’s the deep inverter knowledge coupled with the reliability assessment to ensure you hold the right quantity of each spare part which makes a real difference. Good spares management over the life of an asset can be the difference in project owners losing or saving millions of pounds in revenue and potentially avoiding months of downtime.
In Australia we also recently undertook detailed analysis to inform critical spares purchasing decisions for an 80MW+ solar farm that we manage. The analysis was to inform revised spare parts limits based on actual equipment performance and downtime. Leveraging international experience from our global portfolio, the team in Australia developed a methodology to calculate anticipated failure rates and the associated lifetime. This data was used to identify the benefit of pre-purchasing additional spares to store on site, as compared to ordering additional parts as required, factoring in the cost of lost availability and revenue from potential downtime. The analysis produced recommendations that will save the client more than $5M over the lifetime of the project. Creating further value for our global portfolio, this process can be rolled out to other projects (both wind and solar), using a site’s actual failure data to refine calculations and deliver lifetime value.
The benefits of reliability analysis
In addition, with our years of experience of operating both wind and solar assets, we also recognised that there were various opportunities for the solar sector to learn from the more mature wind sector to improve the performance of operational assets. Whereas most traditional solar O&M strategies focus more on visual inspections, RES’ reliability management service also focuses on diagnostic testing to systematically assess and mitigate risks and compliment the traditional methods. At the end of the Reliability Risk Assessment, owners have a clear picture of the failure risk over the plant lifetime, measured in financial value, and a list of options to reduce the risk including a business case. This proactive approach to maintenance helps to optimise the allocation of maintenance resources, reduce plant downtime and reduce investment in the wrong spares or in activities that add little value. Like wind, using powerful condition monitoring solutions to evaluate and predict deterioration is key to helping reduce downtimes and maximising yield. For instance, with the recent extreme hot weather, we noticed that certain inverter modules were reaching excessive temperatures without any curtailment kicking in, risking a component failure with long downtimes ensuing. Analysis of the data identified clues to this sequence of events enabling us to implement mitigation measures, significantly reducing the risk of failure and site safety.
We are also using advances in technology to find new ways to improve availability. Recent work includes the development of digital twins. For instance, our team in Australia developed a digital twin in collaboration with our global team which is an exact ‘virtual’ model of the site down to string, combiner box and inverter. During the extended COVID-19 lockdowns of 2020 and 2021, the digital twin remotely alerted the asset management team to an inverter underperformance issue whereby the inverter was under-performing by 80% of the expected power. This hadn’t been flagged by the OEM SCADA alarm to notify the O&M contractor. Following receipt and review of automated reporting from the digital twin, we were able to notify the O&M contractor who following an inspection found that due to recent mice plagues, mice had chewed through inverter cabling leading to the underperformance. If the issue had remained undiscovered, the damage would have cost the client $8000 per month and may have taken up to a year to uncover in standard reporting. The leads were fixed, and the site was returned to 100% production within a week reducing the cost of the incident by over 90%.
Repowering, repairing and revamping
With more than 67 gigawatts of solar capacity due to celebrate its twentieth birthday this decade (according to Wood Mackenzie), we will start to see a growth in repowering projects. A large chunk of the capacity is in the European market, where we are seeing some of the first repowering projects.
Across the portfolios we manage, we have found sites with differing onsite technology, unstable equipment for the environmental conditions, lack of quality control on panels and more. These factors dramatically increase the risk of underperformance, more frequent maintenance visits and lengthier faults due to waiting for parts. Resolving these areas quickly and cost-effectively (over the remaining life of the project) is key. Revamping, which involves the intervention and/or upgrading of existing facilities, can help to improve efficiency and/or restore original performance. Examples of revamping include installing panel coating, potential induced degradation (PID) healing and string power optimisers. We have seen yield uplifts ranging from 3 to 10% through reconfiguring module orientation and string design. However, before deciding on whether this is the best option for your project, a careful cost-benefit analysis should be carried out.
Repowering, which involves installing new technology such as modern inverters or bifacial panels, not only ensures that the site will be brought up to a good standard but helps increase generation and improves safety onsite. Take solar modules as an example, in 2010 the average nameplate power output of a standard module was around 290 watts. Today, consumers can expect up to 600 watts for a tenth of the 2010 price and with longer warranties. In the UK&I, we have recently repowered two sites for one of our clients, swapping out central invertors for string invertors, which has resulted in an increase in availability, production, improvements in data visibility and improved safety onsite.
Ultimately, the end-of-life strategy that you select is fundamental to your operational strategy and ensuring you get the most from your assets. For instance, knowing that you are extending the life of an asset will help decisions on the value of component replacements or upgrades to benefit from technology advances and could influence the optimal timing for such works. When it comes to solar projects, the inverters, SCADA, PV modules, framework, even cabling, will all have a different maintenance strategy depending on how many target years remain.
The future is bright
Employment of technologies, such as drones, robots and AI-based digital twins, that had been predominantly overlooked in the past, are now being given serious consideration as O&M teams look to improve plant performances. But also, the softer skills such as keeping a well-stocked spares inventory and having a skilled work force are equally important. Despite the challenges faced over recent years, it has been proven that having a good spares provision and O&M strategy ensures that solar assets continue to perform, and downtime is minimised.