Leistungen
Unsere leidenschaftlichen und erfahrenen Mitarbeiter realisieren weltweit erfolgreiche Projekte für saubere Energie.
Technologien
Wir fördern eine nachhaltige Energiezukunft mit erneuerbaren Technologien neuester Generation.
Erfahren Sie mehr über TechnologienRessourcen
Stöbern Sie in unseren neuesten Informationen. Sie finden hier Nachrichten zum Unternehmen, Kundenberichte, Brancheneinblicke und Forschungsberichte.
RessourcenKarriere
Unterstützen Sie unser Team aus passionierten Menschen, die gemeinsam eine nachhaltige, stimulierende und weltverändernde Arbeit leisten
Mehr erfahrenÜber uns
Wir leben unsere Mission, feiern die Menschen, die sie umsetzen und begrüßen den Wandel, der die Art und Weise verändert, wie die Welt Energie produziert und nutzt
Siehe über unsUnsere Büros
Wie unser Unternehmen sind wir wirklich global - aber mit Stolz lokal. Hier finden Sie Kontakt- und Standortinformationen für jede RES-Niederlassung.
Kontaktieren Sie uns-
Startseite
/
Resources
/
Blog
/
Five ways automation will change the wind industry: from turning autonomous turbines into high performing teams to sending in the bladebots
Five ways automation will change the wind industry: from turning autonomous turbines into high performing teams to sending in the bladebots
by RES | Okt 23, 2023 | Lesezeit: 3 min
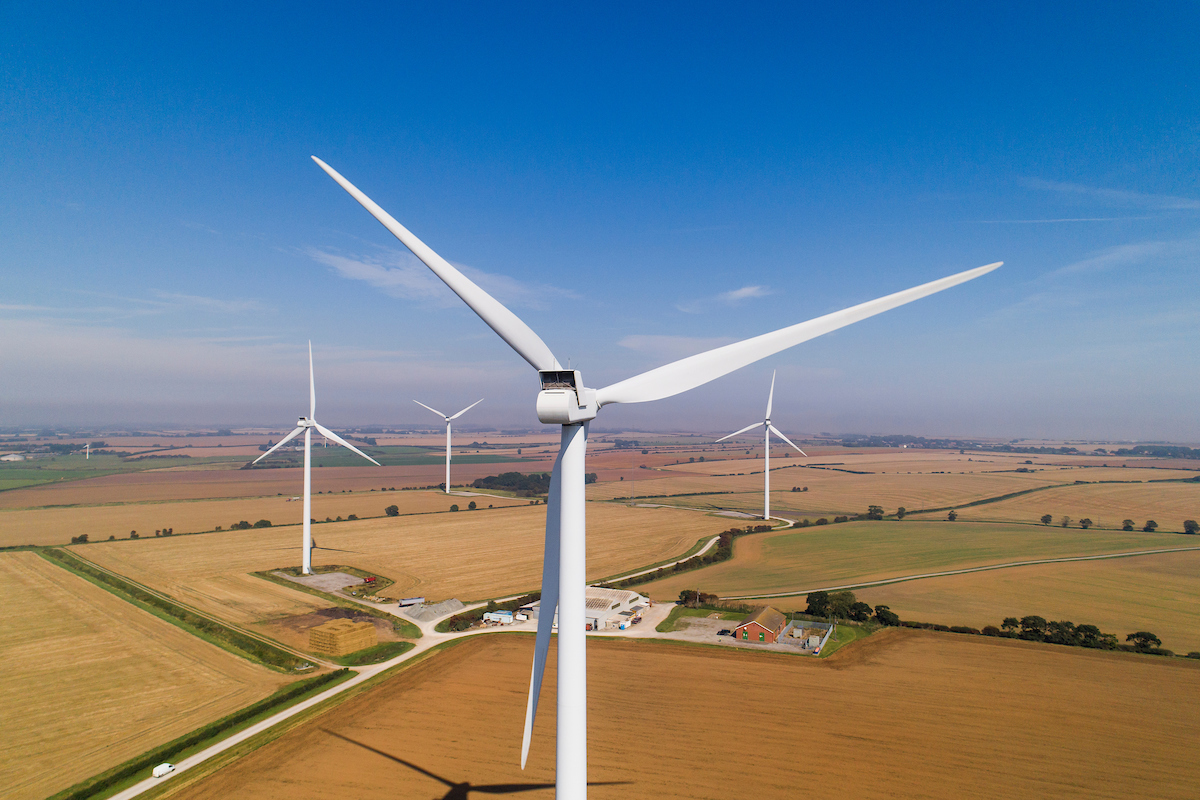
Five ways automation will change the wind industry: from turning autonomous turbines into high performing teams to sending in the bladebots
As technology continues to advance, automation is transforming the energy industry, creating a brighter, more sustainable future. In the wind industry, a focus on optimising operations is creating unprecedented uplifts in power output and performance, while also significantly improving the efficiency and effectiveness of inspection, repairs and maintenance work. Here are just five striking ways that automation is creating positive change in the performance of offshore and onshore wind.
1. Increasing power output with wake steering
Wake steering is a novel wind farm control strategy that aims to increase production by reducing wake loss. Whereas traditionally each turbine optimises itself, wake steering automatically misaligns the upstream turbines to improve performance of the turbines downstream therefore improving power output as a whole.
By operating upstream turbines with a minor yaw misalignment, a net power gain is achieved that creates an energy uplift of between 0.5% and 2% on average[1].
If wake steering had been applied to all global wind farms in 2022, this could have achieved an uplift of between 10.5 TWh and 42 TWh – which would be equivalent to powering a country the size of Denmark or Ireland[2] for the year.
2. Improving yaw alignment and power output with collective control
Collective control optimises power output by having wind turbines share wind direction information, which improves the certainty of the readings used to correct yaw misalignment. Consequently, turbines can yaw more quickly and decisively when wind conditions change.
Preliminary studies suggest an energy uplift of around 0.5% can be expected from collective control – a further 10.5 TWh of electricity – enough to power Estonia[3] for a year. Together with wake steering, collective control provides a new level of accuracy in determining optimum yaw alignment.
3. Automatic shadow flicker recognition
The need to prevent the occurrence of shadow flicker is understood across the industry. Caused when sun light shining directly on residential houses is interrupted by the rotation of a wind turbine’s blades, it historically meant turbines would be shut down at set times to avoid flicker. However, this often led to unnecessary loss of revenue when cloud cover meant there were no shadows being cast.
Using a type of machine learning algorithm architecture called deep neural network RES’ Dynamic Flicker Optimisation System (DFOS) classifies images taken from the site to determine the weather, and automatically decides whether a turbine’s operating mode needs to change to prevent shadow flicker.
4. Enhancing access for blade inspection and repairs using bladebots
AI-assisted blade robots (also known as bladebots) use automation to identify and repair damage to a blade’s leading edge. In some use cases, repairs can be completed up to four times’ faster than via rope access.
Innovative internal wind turbine inspection robots such as IM FutuRe’s NEMO can typically access between 70-80% of a blade’s internal structure where it automatically identifies, photographs, records videos (to create a 3D view) and labels the position of defects in the structural laminate.
Being able to inspect previously inaccessible areas has enabled a leap forward in the preventative inspection and maintenance possible for wind farms.
5. Reducing downtime and fault costs with automation
Advances in automation are improving the way faults are identified, escalated, and addressed, helping to reduce downtime and the considerable associated costs. While there are many automation use cases, the most notable include:
- Automatically determining whether physical intervention is required to correct a fault mode, and resetting and restarting a turbine if not.
- AI-assisted scheduling of technician inspection and repair assignments, with all necessary information collated into one place.
- Identifying the cause of faults, and automatically aligning them to the relevant contracts. This allows contractual KPIs to be generated more easily and accurately.
Automation is spurring a multitude of improvements through the full project lifecycle, helping to reduce costs and downtime, and increasing energy output. With new automation use cases emerging all the time, many more terawatt hours of electricity could be produced without building any new energy infrastructure simply by optimising existing assets and processes.
[1] Assuming that any static yaw misalignment has been corrected first.
[2] https://www.statista.com/statistics/1260553/eu-power-demand-country/
[3] https://www.statista.com/statistics/1260553/eu-power-demand-country/