Solutions
Our passionate and experienced people deliver successful clean energy projects globally.
Technologies
Driving a clean energy future through state-of-the-art renewable technologies.
See all technologiesResources
Browse our latest resources, including company updates, customer stories, industry insights, and research reports.
See all resourcesCareers
Join a collaborative team of passionate individuals who engage in meaningful, stimulating, and world-changing work.
See all careersAbout RES
We live our mission, celebrate the people making it happen and transform the way the world produces and consumes energy.
See about usOur offices
Like our business, we’re truly global – but proudly local. Find contact and location details for every RES office.
Contact us-
Home
/
Resources
/
Case Studies
/
Reducing the lead time for a generator exchange
Reducing the lead time for a generator exchange
by RES | May 15, 2023 | Reading time: < 1 min
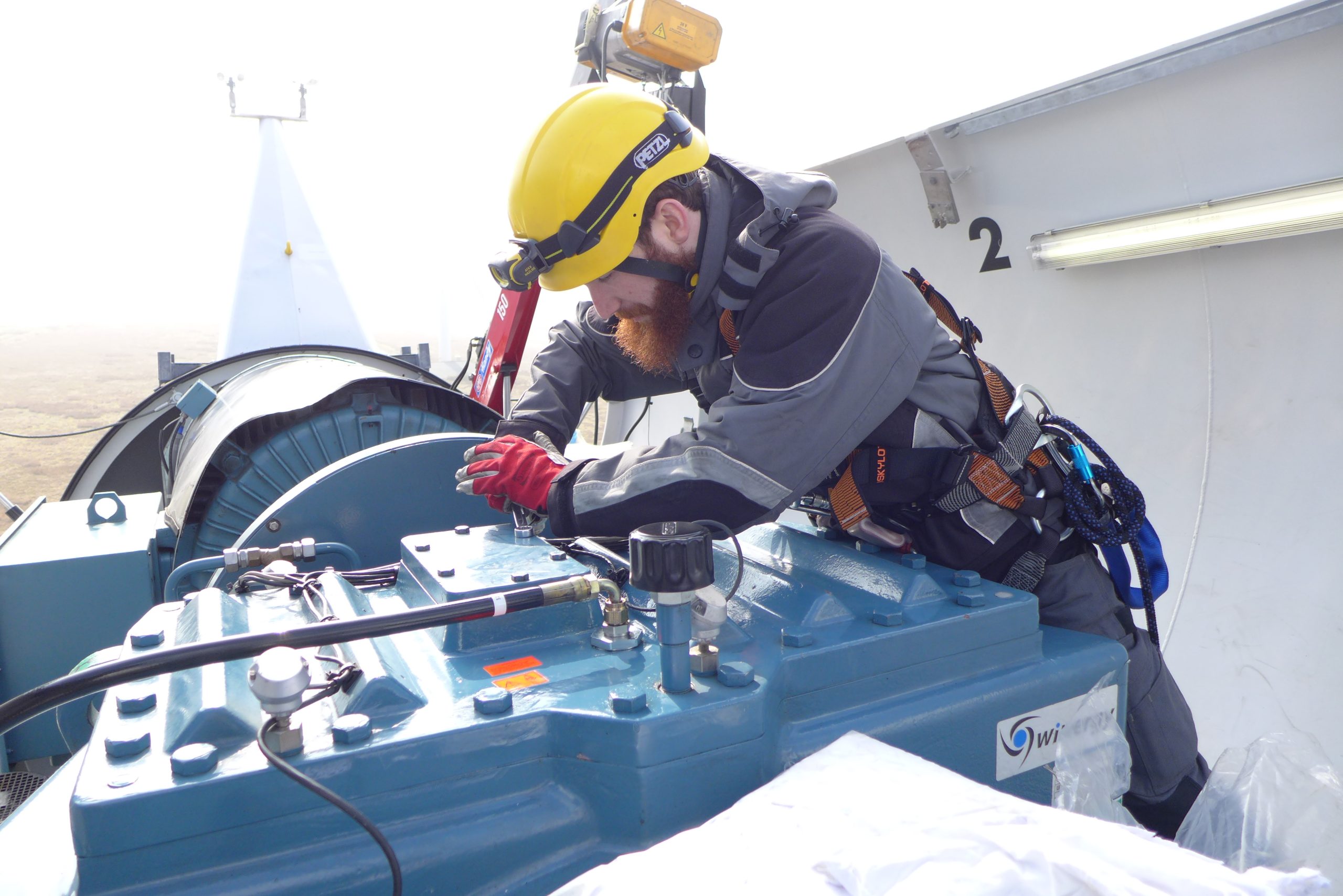
When a generator failed on one of the oldest wind farms in our Asset Management portfolio, RES’ careful planning prevented significant downtime. Due to economies of scale RES is able to procure spares at the lowest cost to the client, and ensure availability.
The work
On this particular site, the turbines aren’t fitted with modern condition monitoring systems, which means our ability to predict failure is diminished, so precautionary measures had been taken in case of faults. The design and specifications for the crane hard-standings had been created in advance to ensure that civil works could begin immediately.
Additionally, a contract was in place with a local generator supplier so that the parts could be sourced straightaway. The replacement generator was brought to site while the RES project management team specified the work required, arranged the contracts and ensured all warranties for the works were in place. RES used its in-house lifting and civil experts as well as our in-house 24/7 Control Centre, to ensure the work was carried out safely.
Results
By strategically planning major component spares, preparing crane hardstand upgrades, and by managing the maintenance from start to finish, we reduced the downtime from potentially 2 months to just 8 days. In this instance we saved the client approximately £14,000 in lost generation.
Our forward planning, monitoring and rapid response often saves clients considerable sums, both in maintenance and lost generation.